Due to the high torque and power density, Axial Flux Permanent Magnet (AFPM) machines are a promising solution for electric vehicles (EVs) and high-efficiency applications. However, the so called pancake motor poses significant challenges to the manufacturing process due to its unusual stator design and the high precision needed for proper rotor placement. This results in high cost and poor volume scalability.
During the thesis internship at Magelec, we developed a scale-up from a prototype to a semi-automated low-capacity assembly line. In particular, the manufacturing and testing steps have been reduced and optimized, applying lean line design techniques. Among the most important issues, resolver-calibration, rotor’s spacer-ring dimensioning and the design of an ergonomic standard workbench are addressed.
Just one year later the line was completed and is producing new motor units.
Thesis and Presentation
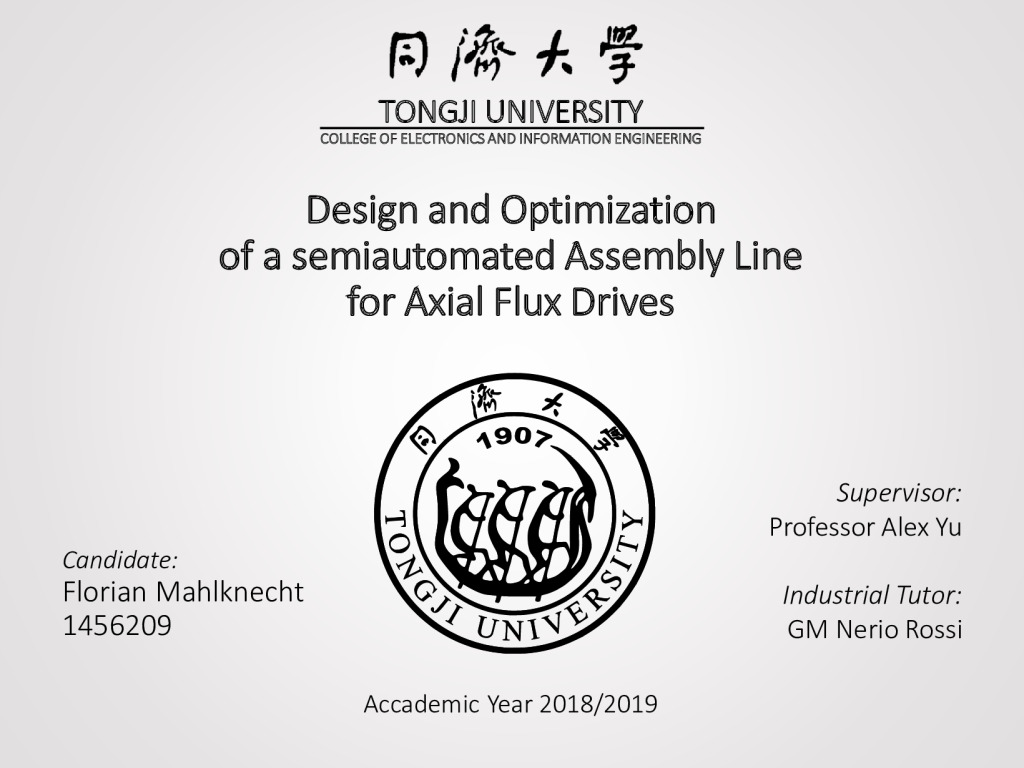
